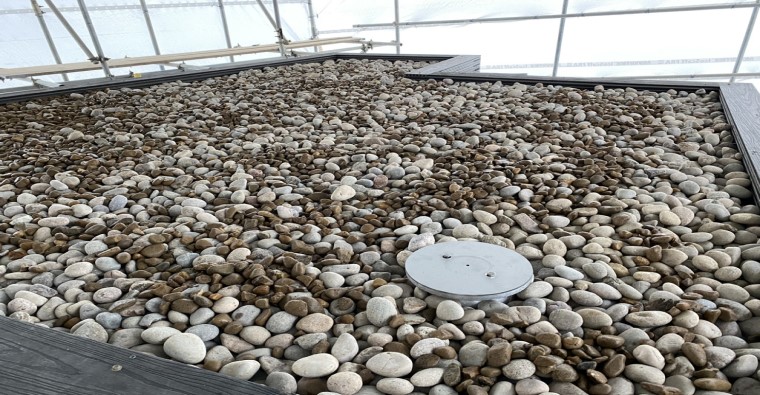
Blue Sky Thinking: ACO and Aquality Create A Blue Roof Like No Other At Queen’s Gate Place Mews
Using its unique RoofBloxx blue roof attenuation system, ACO Building Drainage has combined with Aquality to retrofit a blue roof on an extended building in the middle of London where it was initially thought not possible.
Featuring a cobbled walkway and a grand archway and combined with its status as part of Kensington’s ‘Queen’s Gate’ conservation area, Queen’s Gate Place Mews is one of London’s most sought-after and prestigious places to live. Tucked away off a busy high street, the mews is a collection of quaint residential and commercial properties, with many of the buildings boasting lavish, luxury interiors alongside their retained, quintessentially London façades.
Part of that collection at Queen’s Gate Place Mews is The Lodge. Recently revamped and extended with a new mansard roof to allow for a second storey, one of the key challenges of the project was meeting the SuDS (sustainable urban drainage system) requirement and managing the water runoff from the roof, as set out by the planning committee from The Royal Borough of Kensington and Chelsea (RBKC).
To meet the demand, principal contractors Keystone Construction worked with Aquality and ACO Building Drainage to design and install a unique blue roof attenuation system that sits separately above the roof construction, without adding any risk of water leaking onto the mansard roof itself.
Doing what no others can
With sustainable drainage as a vital factor of the extension being granted approval by the planning committee, Keystone consulted with a number of blue roof manufacturers and roofing contractors to look at how this could be achieved for this unique project. However, all the suppliers Keystone approached had refused the project and stated that it would be impossible, given the small roof area and the necessity of holding the water on the roof’s surface while controlling the rate at which it runs off.
This is where Aquality and ACO stepped in with an approach that no other manufacturers could offer. Using ACO’s innovative patented RoofBloxx attenuation system, this was adapted into a free-standing retrofit application.
Martin Durham, Managing Director and Owner of Keystone Construction said: “We were faced with a very tricky challenge set by the authorities. On one hand, to achieve planning permission, we had to comply by controlling the runoff to prevent flood risks and overwhelming the sewer. However, we couldn’t go forward with a typical blue roof, as holding water on top of a conventional roof invariably adds risk and goes against best practice of roof construction. Water will eventually seep into the roof layers and compromise the structure.
“This was a key reason for choosing to work with Aquality and ACO – as their solution was unlike anybody else’s. By being a standalone system, we could install it on top of the roof build up and it works independently of the roof. Alongside the ingenuity of the system itself, we were very pleased with the design service as well as the ease of the installation too.”
Designed to Last
To help specify the blue roof, Neill Robinson-Welsh, consultant at ACO, worked with Aquality on the hydraulic design of the tank. With a footprint of 13m² and with two layers measuring 30mm each, ACO’s RoofBloxx cell is designed to withstand the ‘once in every 100 years’ extreme rainfall events. It is also intended to account for a 40% climate change and to control runoff at 0.07 litres per second.
The system comprises a free draining edge upstand, the inside of which has a drainage layer placed directly on the gradient roof and on the inside of the upstand. A geotextile membrane was then installed on the top of this layer and the roof fall built out to create a level invert for the open tank that forms part of the ACO patented system.
A geomembrane was then placed inside and detailed at the edges and around the soil pipe, and ACO RoofBloxx Cell units placed inside the liner to create the attenuation void. A further geotextile was placed over top to prevent fine sediment entering the open tank and then cobble ballast was placed on top.
For any rainfall event, water discharges from the tank at the base through the system’s flow restrictor at a controlled rate. The water then runs across and down the sides of the mansard roof into the gutter and away to the sewer system.
Easy Installation, Simple Maintenance
Installation was completed in under a day thanks to the lightweight yet robust ACO RoofBloxx units that can be manually handled and interlocked in a bonded structure.
As well as meeting the SuDS principles, ACO had to ensure the system would be easy to maintain, as with only a 10mm outlet where the surface water drains to, debris could end up blocking the outlet. ACO overcame this challenge by creating an access point to the attenuation tank for regular cleaning and clear out.
Robinson-Welsh said: “When we were approached by Keystone and Aquality, we knew that only our ACO RoofBloxx system would meet the brief. Although the roof area is small, the project has been hugely rewarding and satisfying. This project goes to show how versatile the ACO RoofBloxx attenuation system is.”
For more about ACO RoofBloxx system and to watch the animation of our system, please visit: www.aco.co.uk/products/roofbloxx
Learn more about blue roof design - attend our webinar
To learn more about Blue roof design watch our CPD webinar - Making sustainable urban drainage environments a reality. Register here